The pace of advancements in automotive technology is accelerating rapidly. Despite the enduring presence of combustion automobile engines across generations, the focus on reducing fuel consumption and curbing greenhouse gas emissions has set the stage for the rise of electric vehicles. A recent executive order underscores the significant shift, aiming for half of new cars to be electric or hybrid plug-ins by 2030. In response, automotive manufacturers are intensifying their efforts, betting on a fully electric infrastructure to support their products.
For instance, GFCL EV Products has announced a substantial investment of Rs.6000 Crores over the next 4-5 years to develop EV and ESS batteries, while Adani has committed to installing 75,000 EV charging stations across India by 2030.
The shift toward vehicle electrification has led to a growing demand for autonomous vehicles. As this technology evolves, we can expect electronic sub-systems to become more numerous and complex in order to meet consumer demand. These components have historically been subjected to Environmental Simulation and Reliability Testing in the consumer automotive space.
Automotive manufacturers are required to comply with specific testing mandates to ensure product safety and reliability certification before these technologies can be widely applied in the consumer market.
ENVIRONMENTAL TESTING STANDARDS FOR TODAY’S DEMANDS:
Environmental simulation is a crucial aspect of product testing, designed to replicate the conditions a product will encounter throughout its lifecycle. This is achieved through a series of tests that subject products to varying temperatures, humidity levels, and vibrations. All this is done within the parameters of the intended usage. Once a product has successfully undergone these simulations and met the required standards, it is considered safe for consumer markets.
In the automotive industry, some of the most common tests include temperature and humidity testing, vibration and shock testing, and thermal cycling. These tests are conducted using specialized equipment such as ENVIRONMENTAL/ CLIMATIC TEST CHAMBERS, VIBRATION SHAKERS and THERMAL SHOCK CHAMBERS.
Adhering to industry standards, these tests play a vital role in ensuring the quality and reliability of automotive products before they are released to the market.
TEMPERATURE AND HUMIDITY TESTING:
Various tests can be conducted on either complete vehicles or vehicle sub-systems, including electronic systems, to identify the adverse effects of temperature and humidity extremes.
Examples include rapidly changing temperature tests for electronics enclosures to prevent cracking or warping, as well as moisture condensation in circuits or sensors which could undermine performance. Standards for temperature and humidity testing include
- IEC 60068-2-1 (Low Temperature wake-up)
- IEC 60068-2-64 (Thermal Cycling with Vibration)
- ISO 16750-4 (High Temperature Degradation)
- IS 9000 – 2 (Sec. 1 to 5, 1979, Basic Climatic Test Procedures, Part 2: Cold test Part 3: Dry heat test)
- IS 9000 Part VI (Basic Climate Test, Part 6: Composite temperature/humidity cyclic test)

Rapid temperature and humidity cycling can be efficiently achieved using a range of equipment, such as REACH-IN CHAMBERS and THERMAL SHOCK CHAMBERS. Moreover, larger components or full vehicle systems can be effectively accommodated in WALK-IN OR DRIVE-IN temperature and humidity chambers. It is essential to prioritize key indicators such as temperature uniformity and effective airflow to facilitate optimal heat transfer from the chamber to the product under test. The typical temperature range and rates for these systems are -70°C to 180°C with temperature change rates of 1°C to 25°C per minute.
VIBRATION TESTING:
Combined vibration and environmental simulation testing help provide critical insights into the structural and total reliability of products.
By combining temperature, humidity, and sine or random vibration using mechanical and electrodynamic shakers, users can simulate real-world scenarios such as road vibrations or sudden impacts from potholes. This type of testing allows for a comprehensive assessment of a product’s performance under a variety of environmental and mechanical stressors. Several common standards for vibration testing exist, contributing to the overall qualification process.
- SAE J1211(robustness validation of electric modules)
- GM 3172 (environmental durability for electrical components)
- ISO 16750 (environmental conditions and testing for road vehicles
- IEC 61373 (environmental conditions vibration & shock testing for railway vehicles)
- IEC 60068-2-6 (Sinusoidal Vibration Testing procedure for testing specimens)
- IEC 600068-2-27 (withstand specified severities of non-repetitive or repetitive shocks)
- IEC 600068-2-64 (package testing for structural integrity)
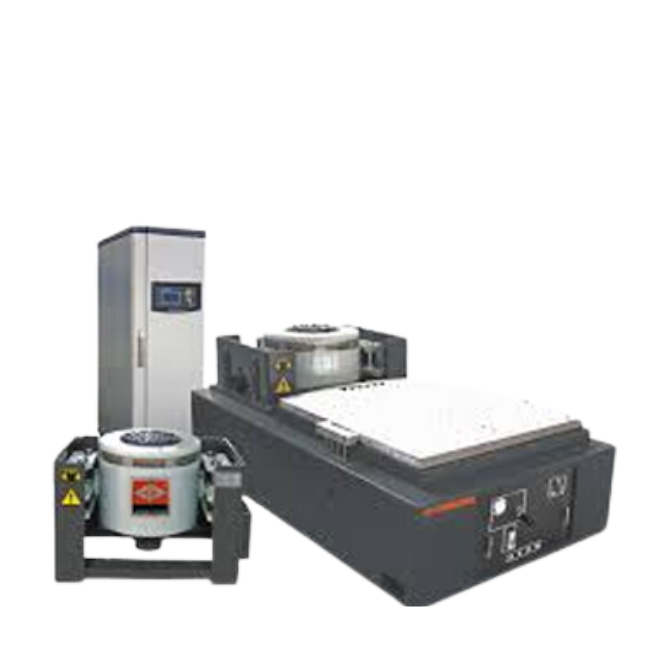
AGREE (Aerospace and General Environmental) Chambers were initially developed for military and aerospace applications, where they were utilized for the simulation of temperature, humidity, and vibration. As the technology evolved, it has been modified to meet the rigorous standards of the automotive industry for reliability and qualification testing. A vibration compatible chamber can be specifically tailored to seamlessly integrate with an existing shaker, allowing for simultaneous performance of temperature, humidity, and vibration tests, with the capability of achieving thermal change rates as high as 25°C per minute.
TESTING FOR THE FUTURE:
As emerging battery and autonomous vehicle technologies gain traction over the next decade, the importance of properly functioning components remains crucial As the automotive industry evolves and consumers rely more on electrified vehicles, the complexity and number of electrical components and systems will continue to increase Therefore, thorough battery testing and environmental simulation of these products will not only guarantee their efficacy, but also lay the groundwork for a safe, reliable, and autonomous driving infrastructure of the future.
Hiacc Engineering has the environmental test chamber to fit your automotive testing needs. CONTACT US today to start a conversation. Our products are designed and built with your products in mind, for over 10 years in Chennai, INDIA.